CNC Water Jet Cutting: The Viable Green Alternative to Other Industrial Cutting Systems
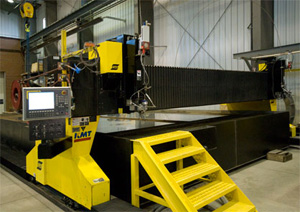
The CNC water jet cutting system easily surpasses today's average run of the mill cutting systems with its high velocity pressurized water jet stream that penetrates and slices through many different materials with unparalleled precision and accuracy. Further still CNC water jet cutters distinguish themselves from other cutting systems in that they are recognized as a green alternative to other systems known to consistently produce hazardous waste materials that require special disposal. Some manufacturers will find the environmentally friendly water jet cutter appealing solely for this reason as there are no additional incurred costs in having to dispose of these hazardous materials.
This relatively new technology has only really been finessed over the last few years with vast improvements made to the software responsible for the operation of the jet head. This has lead to such performance enhancements like the jet head with multi-axis perspectives.
Some water jet cutting applications:
-
Metal fabrication
-
General parts fabrication
-
Rubber gasket production
-
Automotive parts production
-
Aerospace machining
-
mining
-
glass/ceramic and similar textile cutting
-
foam and carpeting cutting
The following list is compromised of materials that have and can be cut by the water jet cutting process:
-
glass
-
foam
-
ceramics
-
laminates
-
granites
-
gaskets
-
wood
-
rubber parts
-
stainless steel
-
bronze
-
aluminum
-
spring steel
-
copper
-
sterling silver
-
nylon
-
acetyl
-
PVC
-
Polycarbonate
-
Brass
-
ABS
-
Polystyrene
-
Fiberglass
-
Titanium
-
Carbon fiber
-
Teflon
Some Added Advantage to Water Jet Cutting
Water jet cutting works through a process of erosion of material produced through the highly pressurized delivery of a stream of water. This process makes the water jet cutting process unique to the industry particularly within the architectural world as it is preferred here over other CNC plasma cutting systems. Water jet cutting is particular useful for two dimensional shaping within a restrictive diameter that falls between a measurement of 0.020 and 0.030 inch jet kerf. These close cutting confines are yet another feature that make the water jet cutter superior to its competitors as it is allows for all parts to be used to their maximum efficiency which is of great advantage when dealing with materials of greater cost. The smoothness of the edge of a material cut by the water jet process varies depending on the model utilized for the job. Generally speaking the water jet cutters can produce rough cut edges whereby the water striation is clearly visible on the surface of the material or a finer cut can be achieved as well by an appropriate model giving the material a smooth cut edge.
In short, the CNC water jet cutter offers high quality performance, ease of operational use, rapid cutting speeds all the while having absolutely no harmful impact on the environment as well as posing zero risk to those in around the area of its operation. As we move forward into the future the improvements to the design and functionality of the water jet are bound to continue with further research being conducted on the possibility of other types of additive abrasive materials as well as other uses such polishing and turning.